Alcast Company - The Facts
Table of ContentsNot known Facts About Alcast Company6 Easy Facts About Alcast Company DescribedThe smart Trick of Alcast Company That Nobody is DiscussingThe Best Strategy To Use For Alcast CompanyAlcast Company Things To Know Before You BuyAlcast Company Things To Know Before You Buy
Chemical Contrast of Cast Aluminum Alloys Silicon promotes castability by reducing the alloy's melting temperature and boosting fluidness throughout spreading. In addition, silicon contributes to the alloy's strength and wear resistance, making it important in applications where longevity is crucial, such as automotive parts and engine elements.It likewise enhances the machinability of the alloy, making it less complicated to refine right into completed items. By doing this, iron adds to the general workability of aluminum alloys. Copper boosts electrical conductivity, making it beneficial in electrical applications. It also boosts rust resistance and adds to the alloy's overall toughness.
Manganese contributes to the toughness of light weight aluminum alloys and improves workability. Magnesium is a light-weight element that offers toughness and effect resistance to light weight aluminum alloys.
Alcast Company - Questions
Zinc improves the castability of light weight aluminum alloys and aids control the solidification process during casting. It enhances the alloy's toughness and solidity.
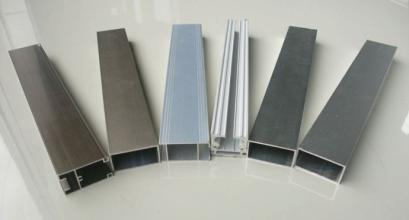
The primary thermal conductivity, tensile stamina, return toughness, and elongation vary. Select ideal resources according to the performance of the target product generated. Amongst the above alloys, A356 has the highest possible thermal conductivity, and A380 and ADC12 have the most affordable. The tensile limitation is the contrary. A360 has the very best return toughness and the highest elongation rate.
Alcast Company - The Facts
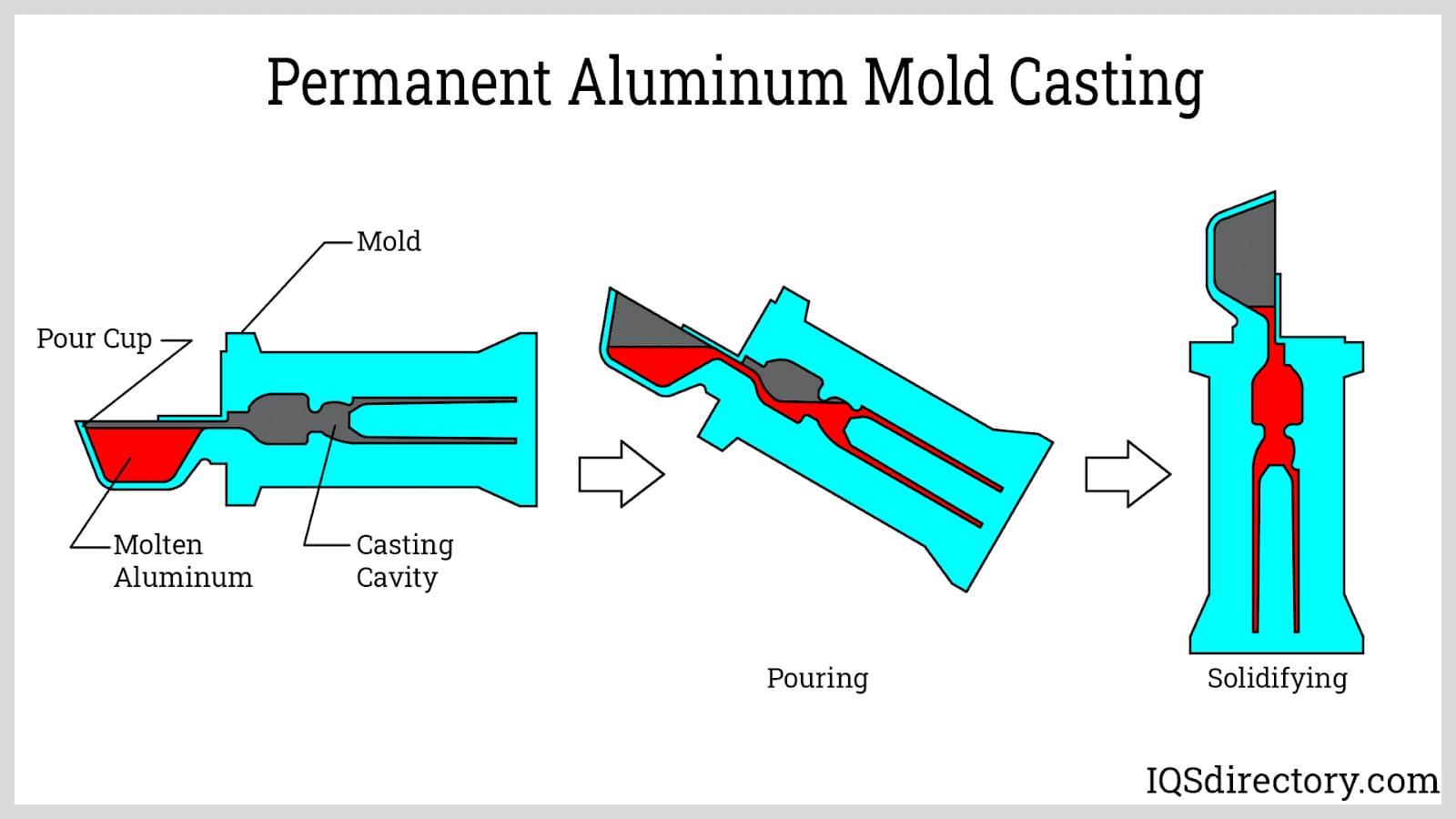
In accuracy casting, 6063 is fit for applications where detailed geometries and top notch surface finishes are extremely important. Instances include telecommunication units, where the alloy's exceptional formability permits for streamlined and aesthetically pleasing styles while keeping structural stability. In the Lighting Solutions industry, precision-cast 6063 components develop stylish and effective lights components that require detailed shapes and good thermal performance.
It brings about a better surface area finish and much better rust resistance in A360. The A360 exhibits premium elongation, making it perfect for facility and thin-walled parts. In accuracy spreading applications, A360 is fit for industries such as Consumer Electronic Devices, Telecommunication, and Power Devices. Its improved fluidity permits for detailed, high-precision elements like mobile phone cases and communication tool housings.
Alcast Company for Beginners
Its one-of-a-kind properties make A360 a useful choice for accuracy casting in these markets, boosting item durability and quality. Light weight aluminum alloy 380, or A380, is an extensively used casting alloy with a number of distinctive qualities. It supplies excellent castability, making it a suitable choice for precision spreading. A380 shows good fluidity when molten, making certain elaborate and comprehensive mold and mildews are properly reproduced.
In precision spreading, light weight aluminum 413 radiates in the Consumer Electronic linked here Devices and Power Devices sectors. It's generally utilized to craft complex parts like mobile phone housings, camera bodies, and power tool casings. Its accuracy is exceptional, with limited resistances up to 0.01 mm, making certain remarkable item assembly. This alloy's exceptional deterioration resistance makes it an excellent selection for exterior applications, making certain durable, resilient items in the stated markets.
Rumored Buzz on Alcast Company
The aluminum alloy you choose will significantly affect both the casting procedure and the residential or commercial properties of the final item. Because of this, you should make your choice very carefully and take an enlightened method.
Determining the most suitable light weight aluminum alloy for your application will imply evaluating a broad variety of features. The first category addresses alloy features that influence the production procedure.
More About Alcast Company
The alloy you select for die casting directly affects numerous elements of the spreading process, like just how simple the alloy is to collaborate with and if it is susceptible to casting issues. Hot cracking, likewise referred to as solidification fracturing, is a regular die casting flaw for aluminum alloys that can cause interior or surface-level rips or cracks.
Specific aluminum alloys are much more prone to hot cracking than others, and your selection must consider this. An additional common flaw discovered in the die spreading of light weight aluminum is die soldering, which is when the actors sticks to the die wall surfaces and makes ejection hard. It can harm both the cast and the die, so you ought to search for alloys with high anti-soldering buildings.
Corrosion resistance, which is already a significant feature of aluminum, can differ significantly from alloy to alloy and is a crucial characteristic to think about depending upon the ecological problems your item will be subjected to (Foundry). Wear resistance is one more building frequently looked for in light weight aluminum items and can set apart some alloys